Цинкование металлоконструкций
Линия горячего цинкования предназначена для нанесения защитных коррозионностойких покрытий на следующие виды изделий:

- несущие фермы перекрытий и опорные колонны зданий, металлоконструкции различного типа;
- конструкционные профили из стали;
- дорожные ограждения;
- профили из углеродистой стали для опор линий электропередач;
- элементы ограждений.
Линия содержит два технологических потока, позволяющих обрабатывать изделия с максимальными размерами (максимальные внешние габариты):
- основной технологический поток — 12,5 x 1,4 x 2,7 м (максимальные, внешние габариты по контурному контролю);
- поток негабаритной (длинномерной) продукции 16,5 x 1,4 x 2,7 м.
Расчетная часовая производительность линии 10,0 т/ч. Соотношение поверхности и веса цинкованных металлоконструкций 20,0 кг/м2 (при средней толщине стенок металлоизделий 5,0 мм).
Использование горячо цинкованных покрытий позволяет снизить скорость коррозии в 40 - 50 раз в сравнении со скоростью коррозии черного метал- ла, что позволяет увеличить срок службы металла до 80 лет.
Качество продукции на высоком уровне достигается благодаря использованию передовых технологий в производстве, а также применению сырья и материалов от европейских поставщиков.
Процесс горячего цинкования осуществляется автоматически по специальным программам, разработанным специально для нашего предприятия. Эти программы определяют последовательность и продолжительность технологических операций в зависимости от характеристик материала.
Контроль за составом и технологическим режимом рабочих растворов осуществляется с центральной панели управления линии с помощью специальных датчиков, установленных в ваннах предварительной подготовки поверхности.
Корректировка растворов происходит автоматически. После получения команд от АСУ открываются запорные клапаны на участке приготовления растворов, и необходимый реагент дозируется в соответствующую ванну.
Регулярный анализ состава расплава ванны цинкования проводится с помощью эмиссионного спектрометра.
По согласованию с заказчиком может быть проведена дополнительная предварительная подготовка поверхности изделий в виде дробеструйной очистки.
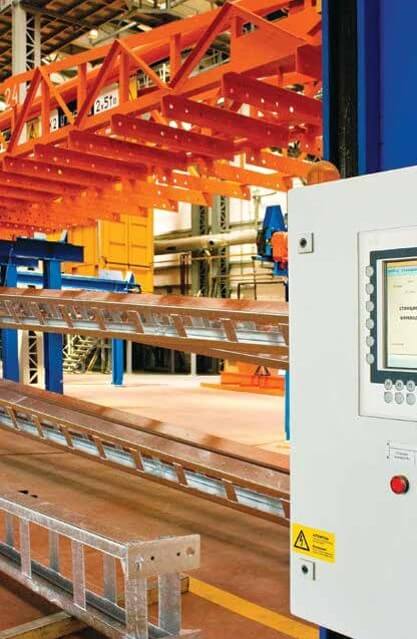
Процесс горячего цинкования
Производственный процесс завода горячего цинкования на предприятиях группы ФерроЦинк включает следующие основные этапы:
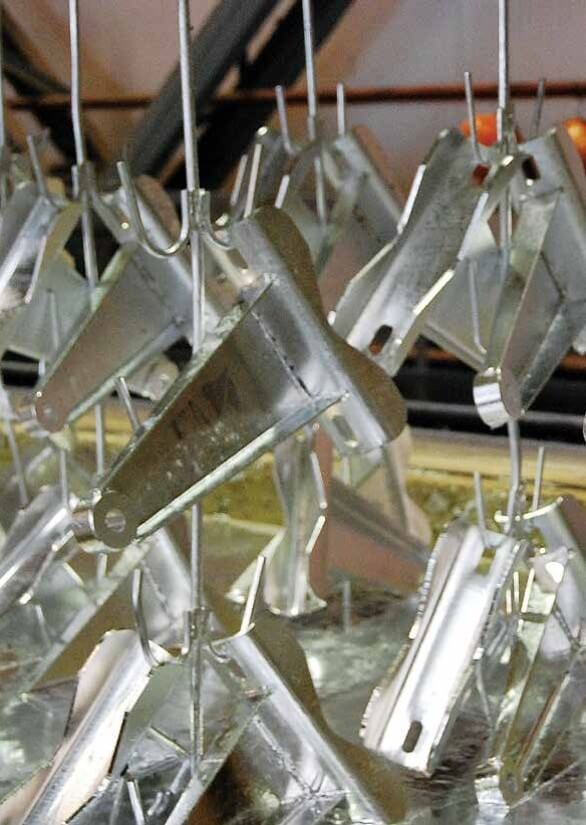
- Подготовка поверхностей для цинкования.
- Цинкование металлоконструкций.
- Охлаждение металлоконструкций.
- Операции контроля качества выполняемых работ.
1. Подготовка поверхностей для цинкования
Подготовка поверхности должна обеспечить сцепление наносимого ме- таллического защитного покрытия с металлом основы. При этом наличие даже небольшого количества загрязнений препятствует сцеплению. Любые нарушения и несоответствия на этапе подготовки поверхности будут видны при извлечении стали из расплавленного цинка, так как грязные участки останутся без покрытия. На этом этапе устраняются загрязнения, которые могли бы препятствовать реакции цинк-железо.
Подготавливаемые к дальнейшей цинковке металлоконструкции поме- щаются в ванны для прохождения процессов обезжиривания, травления, флюсования.
Очистка от жиров
На первом этапе обработки поверхности деталей необходимо удалить все масляные и жировые загрязнения. Для этого используется специальный раствор, который нагревается до высокой температуры и наносится на детали.
Затем следует этап травления
После очистки поверхности от жиров необходимо удалить все оставшиеся загрязнения, такие как оксиды, ржавчина и каламины, которые могут образоваться в процессе волочения и прокатки. Для этого детали погружаются в раствор соляной кислоты.
После травления необходимо тщательно промыть детали, чтобы удалить остатки соляной кислоты и солей железа. Это позволяет подготовить поверхность к следующему этапу — флюсованию.
Флюсование
После травления и промывки детали погружаются в раствор флюса, который содержит хлорид цинка и хлорид аммония. Флюсование проводится «сухим» способом.
Цель флюсования — удалить невидимые плёнки окислов с поверхности деталей. Также происходит удаление или диспергирование солей железа и углеродсодержащих загрязнений, оставшихся на поверхности. Флюс активирует поверхность, обеспечивая связь между основным металлом и цинковым покрытием.
В процессе флюсования образуется равномерная плёнка, которая предотвращает окисление до погружения в расплав цинка и улучшает реакцию цинк-железо.
После флюсования детали перемещаются в сушильную печь для предварительного нагрева.
На нашем предприятии используется прогрессивная европейская технология флюсования, которая позволяет поддерживать концентрацию железа во флюсе на нулевом уровне. Это снижает образование гартцинка и, соответственно, себестоимость продукции.
Сушка и предварительный нагрев
Процесс сушки и предварительного нагрева деталей способствует ускорению реакции и сокращению времени погружения в расплав цинка. Это достигается за счёт уменьшения тепловой инерции и снижения разбрызгивания цинка из-за разницы температур.
Сушка осуществляется в сушильной камере прямого нагрева, которая оснащена системой регенерации тепла. Эта система является продолжением зоны химической обработки и соединена с ней с помощью торцевых дверей.
Сушильная печь представляет собой закрытое пространство, в котором транспортная система перемещает траверсы с подвешенными на них металлическими изделиями. Печь соединена с корпусом защитно-вытяжного короба ванны цинкования.
В сушильной камере могут одновременно находиться две траверсы. Время пребывания изделий в печи рассчитано так, чтобы максимально эффективно использовать её возможности.
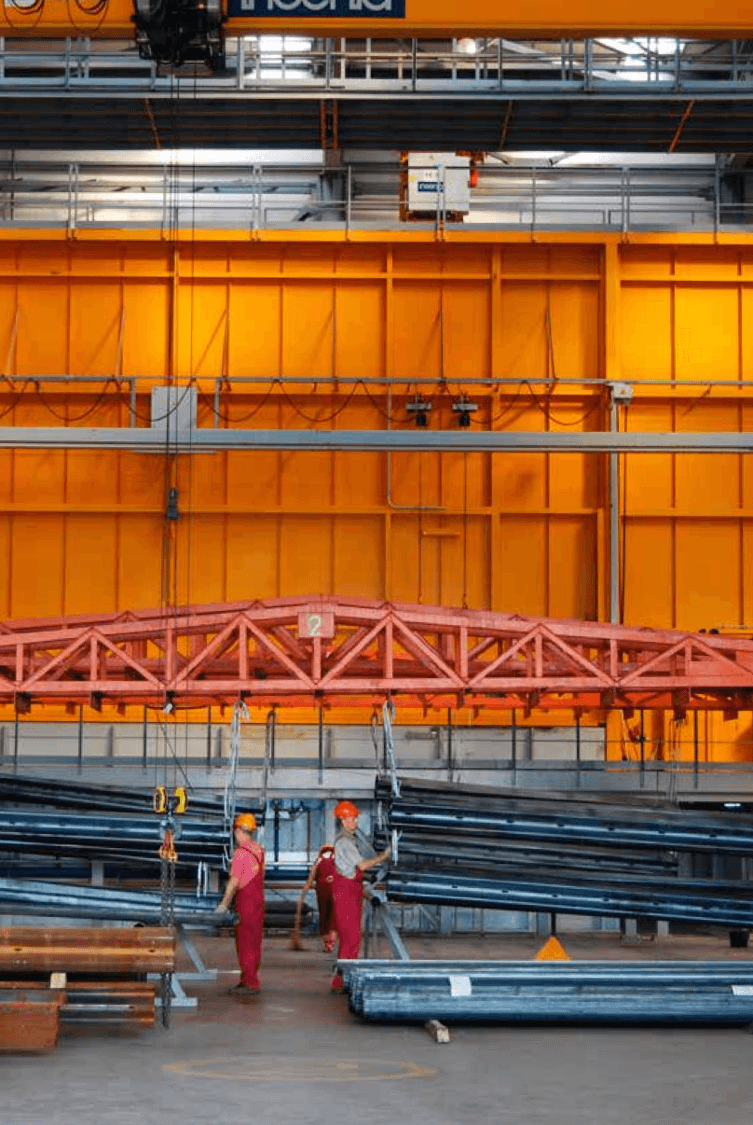
Когда изделия выходят из печи, их температура составляет 90–100 °C. На поверхности стали остаётся тонкий слой солей флюсования, и детали готовы к погружению в расплав цинка.
После того как изделия подготовлены, их погружают в цинк. Это ключевой этап всего процесса.
Перед тем как изделия погрузить в ванну цинкования и извлечь из неё, поверхность ванны тщательно очищают от окислов и остатков флюсования.
2. Цинкование металлоконструкций
Детали, подлежащие цинкованию, погружаются в расплавленный цинк, чистота которого составляет не менее 98%, при температуре от 440 до 460 °C. Скорость погружения зависит от размеров и формы деталей.
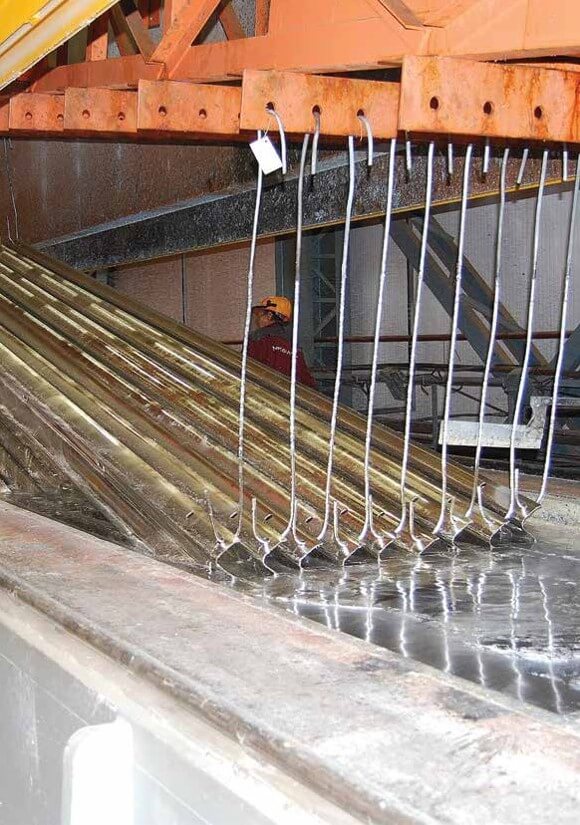
Температура кипения хлоридов, входящих в состав флюса, значительно ниже температуры расплава цинка. Поэтому при контакте с ним они испаряются, оставляя после себя идеально чистую поверхность.
Летучие соединения, образующиеся при разложении флюса, способствуют механическому удалению загрязнений с поверхности ванны и создают нейтральную атмосферу в месте погружения изделий в расплав.
Верхний слой покрытия, образующийся во время извлечения изделия из расплава, состоит из чистого цинка. Именно он придаёт изделию блестящий вид сразу после цинкования.
Реакция Fe + Zn продолжается и после извлечения изделия из расплава до тех пор, пока температура цинкованных деталей остаётся достаточно высокой для процесса диффузии.
Для придания изделиям дополнительных декоративных свойств и защиты от белой ржавчины в состав ванны цинкования добавляют специальные добавки в виде сплава.
3. Охлаждение
Цикл завершается после извлечения изделий из цинкового расплава путем охлаждения на воздухе.
4. Операции контроля за качеством выполняемых работ
Автоматическая система управления позволяет в режиме реального времени контролировать показатели производственного процесса:
- входной контроль качества применяемых материалов;
- постоянство концентраций и режимов работы растворов;
- температуру расплавленного цинка;
- скорость погружения и извлечения;
- длительность погружения;
- толщину слоя получаемого покрытия;
- адгезию слоя цинка к металлу / прочность сцепления покрытия.